How Greyhound optimized driver scheduling automation and optimization
In the world of transportation, it’s difficult but necessary to transition from manual scheduling systems to meet new, real-world constraints and achieve business goals. We automated and optimized driver scheduling for Greyhound while reducing operating costs and increasing driver job satisfaction.
60%
Reduction in Six-Day Work Weeks
33%
Reduction in Planned Extra Boards
5%
Reduction in Layover and Driver Idle Tim
Business problem
With a large network of more than 1,000 buses, 4,000 bus stops and 1,800 drivers, Greyhound requires feasible driver schedules to staff every bus while addressing driver shortages, regulatory constraints and driver lifestyle preferences. Driver scheduling had always been a tedious, manual and myopic process, resulting in high costs for extra board drivers and irregular assignments, contributing to poor driver retention. Greyhound collaborated with Optym to create and implement DriverPlan, a driver schedule optimization system that automates the scheduling process, reduces the need for extra board drivers and improves the quality of driver assignments.
Our approach
We developed a three-stage approach to solve the problem efficiently: 1) we created the possible sequences of bus driving assignments, called tours; (2) we created favorable tour patterns for different on-duty and off-duty arrangements; and (3) we chose the optimal selection of patterns to cover all driving assignments.
At each stage, we considered multiple objective function factors, union and regulatory rules and implementability requirements. We worked in close collaboration with the driver planning group at Greyhound to ensure that tacit knowledge was included in the optimization model, the model solutions were implementable and the system was easy to configure. We illustrated results to end users with a business intelligence tool for detailed analysis and agreed on the final configuration.
Key benefits
- Our model demonstrated a 60% reduction in six-day work weeks without compromising on driver wages, leading to higher driver satisfaction and retention.
- The model created more regular driver schedules, resulting in a 33% reduction in extra boards.
- Our model reduced layover and driver idle time costs by 5%.
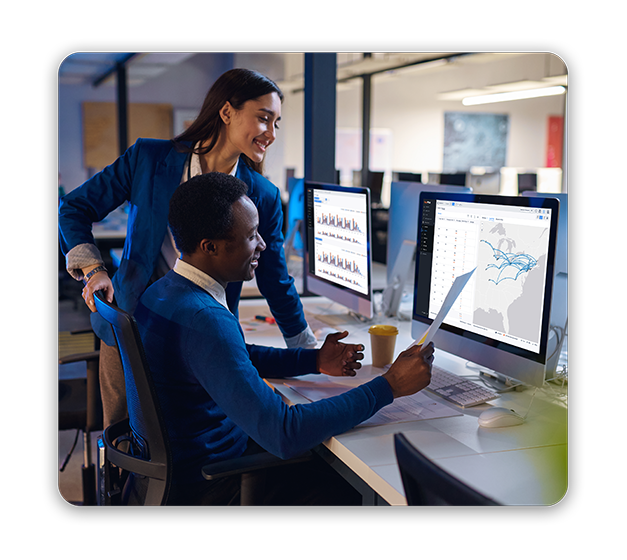
The solution
As a long time user of HaulPlan, Saia knew their way around the system when the unexpected struck. While purpose-built for linehaul planning and optimization, Optym’s technology enabled Saia to maintain advanced agility, which easily transferred over as an emergency planning tool.
Saia took advantage of various optimization modes, which allowed for studies for diverting shipments from one terminal to another specific terminal, selecting the next best terminal in hub skip mode. As terminals would quickly need to be dropped from the network, Saia was able to quickly adjust.
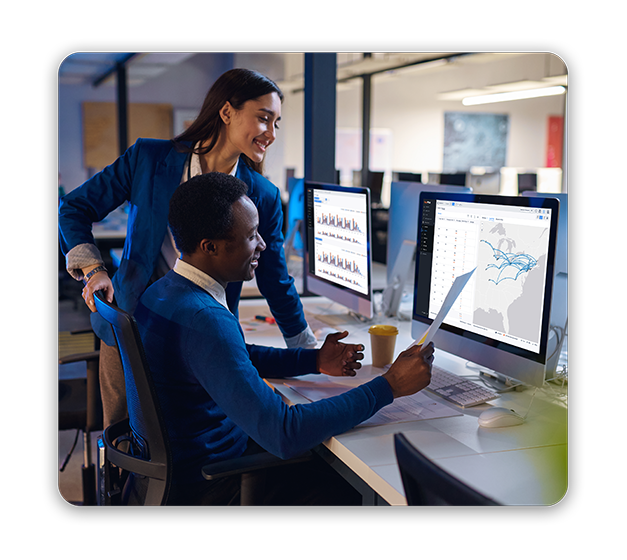
The solution
As a long time user of HaulPlan, Saia knew their way around the system when the unexpected struck. While purpose-built for linehaul planning and optimization, Optym’s technology enabled Saia to maintain advanced agility, which easily transferred over as an emergency planning tool.
Saia took advantage of various optimization modes, which allowed for studies for diverting shipments from one terminal to another specific terminal, selecting the next best terminal in hub skip mode. As terminals would quickly need to be dropped from the network, Saia was able to quickly adjust.
Results
Planners were able to create optimized driver plans within 15 minutes after the data was prepared and then study the impact, a dramatic improvement in the planning process. Thanks to rapid design and development in agile mode, we were able to help Greyhound create implementable, optimized schedules within eight months of beginning the project. And as a result of our efforts, the DriverPlan Optimization Group at Greyhound earned runner-up at FirstGroup’s 2018 Be First Awards for its significant contributions to making the company more efficient.
Results
HaulPlan allows carriers to thrive in the face of uncertainty, showcasing the effectiveness of technology in mitigating the impact of external disruptions.
With HaulPlan in place, Saia successfully prepared for an unexpected event and navigated the challenges brought about by COVID-19 in a way that best served employees and customers.
“HaulPlan has empowered our planners to easily see the network impact of our decisions, design temporary weather or COVID impacted alternatives, and seamlessly push our changes into our execution system, saving us and our customers time and money,”
Jeff Owen
Vice President of Linehaul Operations